The chemical etching process is becoming more and more advanced with the help of technology. The primary application of a chemical etching process is manufacturing precision components through complex machining techniques. Almost all metals can be used in this particular method to create precision components as per the need of the industry.
There are multiple benefits that are offered with this technique and most of them are influenced through extensive use of technology. In this article, we will be talking about how chemical itching is benefiting from adequate use of advanced technology. But first, let us get an idea of what chemical etching is.
The Definition
Chemical etching is a method where a sheet metal is used to etch an image or a logo onto a photoresist. This basic pattern is then printed or laminated on a metal sheet which can be of any material. The distinguishing feature of this method is that the photo on which there is no print is removed with precision.
This leaves a clear design on the material and helps with accuracy on different metal parts. As it is obvious, technology is used to create a well-defined pattern on the metal sheet for high precision.
The Benefits of Technology
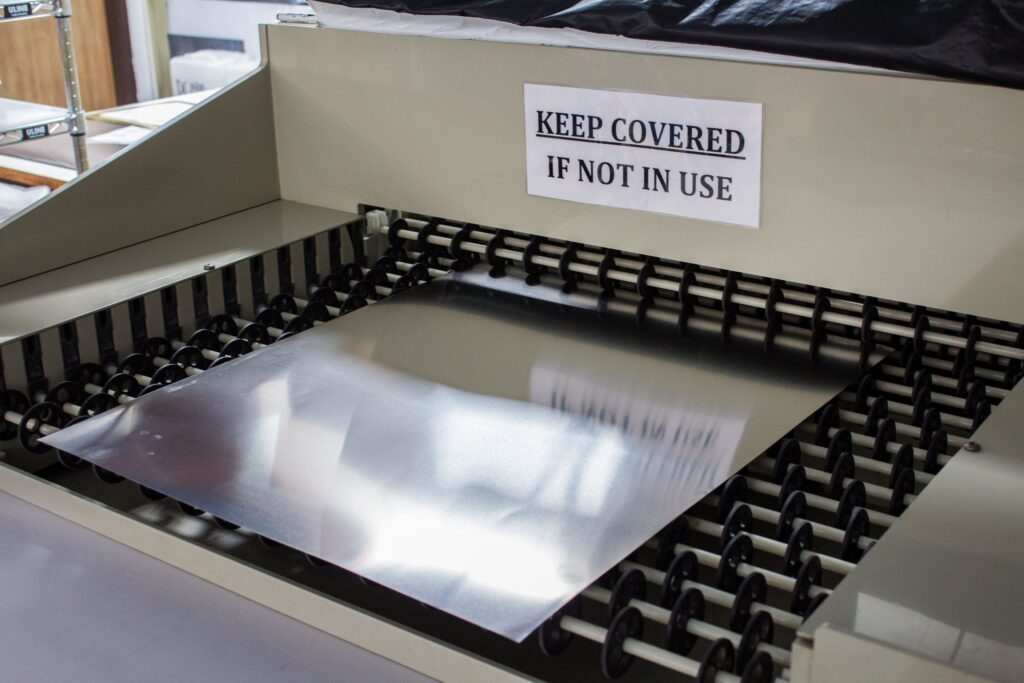
Source: uweinc.com
Technology has multiple benefits when it comes to chemical etching for multiple metals irrespective of applications. Here are some of them:
Micron Accuracy
The primary benefit that technology offers this process is achieving micron accuracy. Micron accuracy means that extremely detailed patterns and designs would be easy with the help of machinery made to do the same. Sometimes the print to be etched is meant to be very small like for serial numbers.
In such a case, one requires advanced technology that will deal with complexity without any hiccups or errors. In bigger facilities that provide mass production, all of the metal components are printed at the same time. During this process, all of the machines are involved in the same manner and will participate in high accuracy without any deviation from one part to another.
Cost Effectiveness
With the development of technology which is specifically made for chemical etching, manufacturers have come up with cost effective processes. The idea behind cost effectiveness aims at reducing costs for the manufacturer as well as for the customers who will be looking for the service.
Since most of the tooling has gone digital technology has also helped in making the process more convenient. The manufacturers no longer require heavy tool assemblies in order to complete the demands for printing.
High Complexity
We have already established that advanced technology works to reduce costs of assembly and maintenance. Another advantage of technology is that it can handle complex designs and printing without any additional complications. During the process, there are multiple factors that dictate how well the result would go. Good machinery with advanced technology will be easy to use in different components with different geometries.
The high complexity feature of new machinery is that the manufacturing would be complete without any added costs. Complexity is also reviewed in terms of how the metal is removed after the photoresist is applied on the surface. Advanced machinery removes the metal simultaneously which reduces cost and also increases efficiency in terms of how soon that entire method is finished.
Compatibility with Different Materials
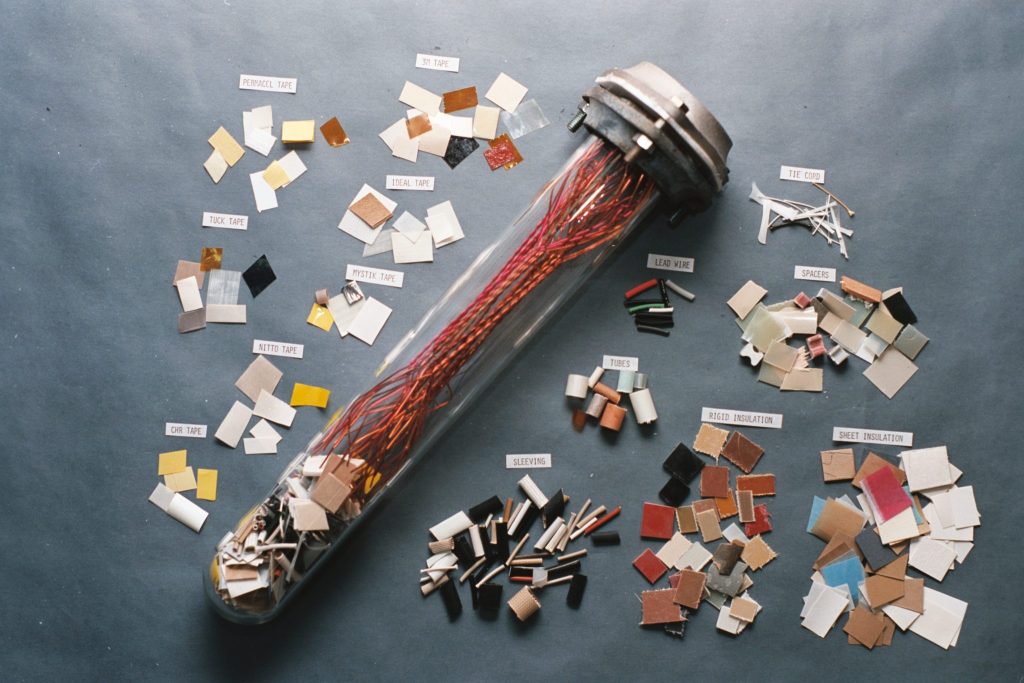
Source: elteklabs.com
If there is one thing which needs to be understood at the time of chemical etching, it is how metals would react to it. Typically the machinery has been developed in such a way that different metals of different grades are compatible with the machinery. The compatibility, therefore, is only dependent on their thickness.
Almost all metals used for manufacturing industrial components are well suited for this technique as long as their thickness is between 0.01 to 1.5 mm. The applicability of this method is for reaching which can be explained by the use of nearly 2000 metal types. Metal chips are used every year by multiple suppliers across the globe. The following metal types are most commonly used in this process:
- Nickel and its alloys
- Titanium and its alloys
- Steel and Stainless steel
- Copper and its alloys
- Molybdenum
- Polyimide Metallized Film
- Aluminum
The right technology takes into account how different metal grades will be reacting to the process and whether the thickness will be impacted during the etching.
Stress and Burr-free
It is important to mention this benefit because it is directly related to how the metals chemical properties are left unaltered. As compared to the technology used in waterjet cuts or lasers, chemical etching is relatively good for reducing degradation of the metal. Even stamping might cause some distortion in the material grade but chemical etching is done with the help of technology which leaves it burr and stress free.
It is perfect for applications across different industries, especially the ones dealing with different chemicals. Any use in which metals are required depend on no reaction with the materials in which they will be coming in contact. The somewhat inert nature is protected with the help of the right machinery across different material grades.
Components For Chemical Etching
To understand the full range of technology in the chemical etching process, one also needs to know which components are printed. So, the components include bipolar plates, lead frames, plate heat exchangers, motor laminations, shims, gaskets, automotive interior trim, medical devices, filters, sieves, springs, flextures and diaphragms.
The Takeaway
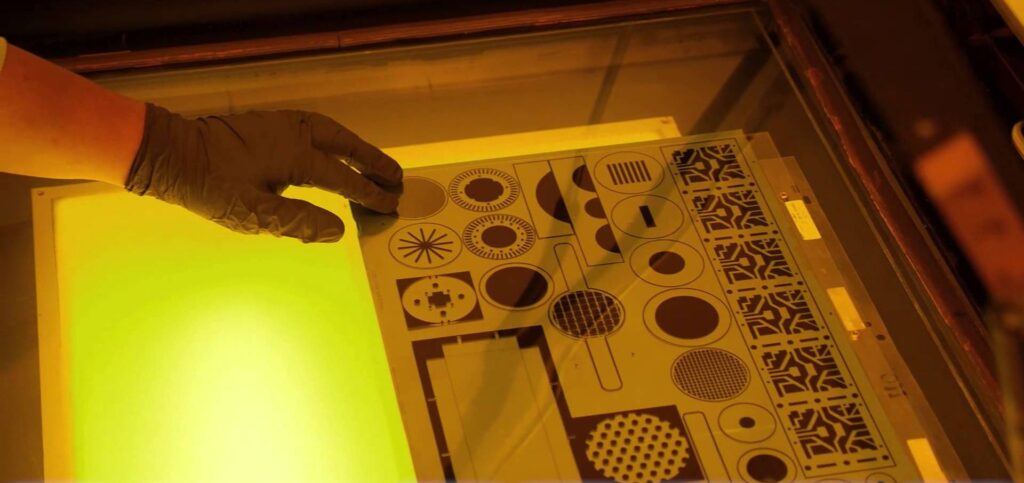
Source: uweinc.com
The chemical etching process is dependent on technology for precision and minimal degradation of the metal grade. Deficiency of the method also helps in reducing the costs and making it more reliable for mass printing.
The chemical properties of a material is not impacted if the right technology is used for etching. Accuracy and precision up to microns is possible if the right machinery is used. Because of complete resistance to any kind of degradation more than 2000 material grades can be used for this process across different industries.