Stainless steel shot is widely used in shot blasting applications for surface cleaning, preparation, and finishing. It is an effective abrasive that removes contaminants, polishes metal surfaces, and enhances durability without causing excessive wear or contamination. However, choosing the right stainless steel shot is crucial to achieving the best results. Factors such as shot size, hardness, and application type must be carefully considered to ensure optimal performance and efficiency.
Understanding Stainless Steel Shot
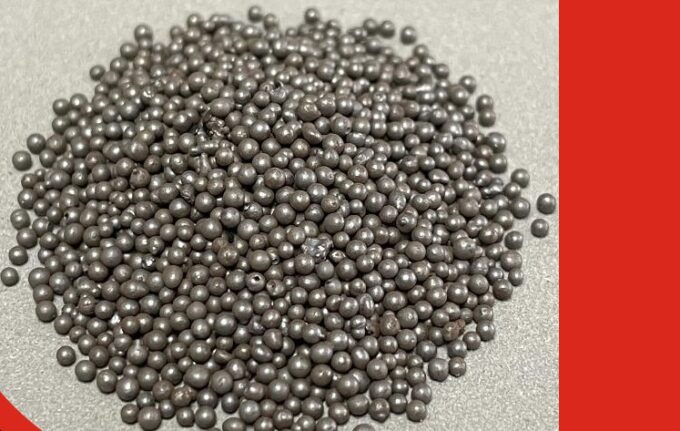
Source: coniex.com
Stainless steel shot (in Spanish this is known as granalla de acero inoxidable) consists of spherical or conditioned cut wire particles made from stainless steel alloys. Unlike carbon steel abrasives, it is corrosion-resistant, long-lasting, and does not leave behind ferrous contamination. This makes it particularly suitable for applications where cleanliness and precision are essential, such as in the aerospace, medical, and food processing industries.
Factors to Consider When Choosing Stainless Steel Shot
- Shot Size and Shape
The size and shape of the stainless steel shot impact the level of surface roughness and the efficiency of the cleaning process. Larger shot sizes provide more aggressive cleaning and surface texturing, making them ideal for heavy-duty applications such as removing rust, scale, and old coatings. Smaller shot sizes, on the other hand, are better suited for precision cleaning, polishing, and achieving a smoother surface finish. - Hardness and Durability
Stainless steel shot is available in different hardness levels, typically ranging from softer grades (Rockwell C 40-50) to harder grades (Rockwell C 55+). The hardness of the shot determines its impact force and longevity. For delicate materials or components requiring a polished finish, a softer stainless steel shot is recommended. For tougher cleaning applications that require high-impact force, a harder grade will be more effective. - Material Composition
The alloy composition of the stainless steel shot affects its wear resistance, longevity, and suitability for different applications. Common grades include:
- Austenitic Stainless Steel Shot (300 Series): Provides excellent corrosion resistance and is ideal for blasting non-ferrous metals like aluminium and brass.
- Martensitic Stainless Steel Shot (400 Series): Harder and more durable, suitable for aggressive cleaning of ferrous metals and hard surfaces.
- Application Requirements
Different industries and applications require specific types of stainless steel shot. Consider the intended use before selecting the right abrasive:
- Surface Preparation for Coatings: If the goal is to improve paint or coating adhesion, a medium to coarse stainless steel shot provides the necessary surface roughness.
- Polishing and Cleaning: For achieving a smooth, uniform finish, fine-grade stainless steel shot is recommended.
- Deburring and Peening: If the application requires removing burrs or strengthening metal surfaces, a controlled shot peening process with high-hardness stainless steel shot should be used.
Choosing a Reliable Supplier
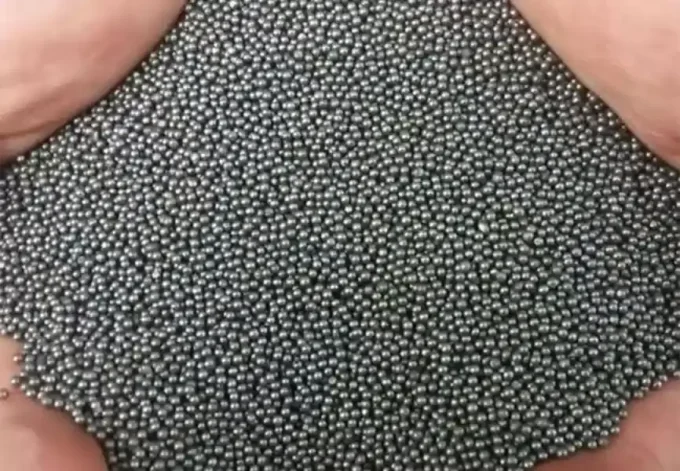
Source: airoshotblast.in
Working with a trusted stainless steel shot supplier ensures consistency, quality, and cost-effectiveness. A good supplier should provide a range of shot sizes and hardness levels, along with expert advice on selecting the best option for your specific application.
Conclusion
Choosing the right stainless steel shot is essential for achieving optimal surface cleaning and preparation. By considering factors such as shot size, hardness, material composition, and application requirements, businesses can improve efficiency, extend the lifespan of their blasting media, and ensure high-quality results.